The Cartographer’s Mark: Identifying Regional Variations in Typewriter Ribbon Production
The satisfying *thwack* of a typewriter key striking the platen, the gentle whir of the carriage return – these are sounds steeped in history, whispering of letters penned and stories told. While we often admire the elegant machinery of antique typewriters, a crucial, often-overlooked element contributes profoundly to their character: the ribbon. These long, often fragile strips of fabric, coated with ink, are far more than mere office supplies; they are historical artifacts, bearing the silent marks of their origin and the hands that produced them. Understanding the nuances of typewriter ribbon production – the regional variations, the subtle shifts in color and material – is akin to deciphering a cartographer’s mark on an ancient map, revealing a fascinating tapestry of industrial craftsmanship.
The Early Days: American Ingenuity and European Precision
The evolution of the typewriter ribbon is intrinsically linked to the typewriter itself. Early models, pioneered by figures like Christopher Latham Sholes, used simple silk ribbons, often dyed a dark brown or black. These ribbons were notoriously uneven in ink distribution and prone to breakage. The late 19th and early 20th centuries witnessed a rapid expansion of typewriter manufacturing, both in America and Europe. American companies, known for their mass production techniques, initially focused on affordability and efficiency. European manufacturers, particularly in Germany, England, and France, often prioritized higher quality materials and more intricate production processes.
The shift from silk to a more durable satin weave proved revolutionary. American ribbon manufacturers, like Smith Corona and Underwood, began producing ribbons on a larger scale, utilizing cotton satin as a cost-effective alternative. However, the quality often varied. European ribbons, frequently manufactured in workshops utilizing traditional methods, often displayed a richer, more consistent ink saturation and a more elegant feel. The subtle differences weren’t just aesthetic; they impacted the longevity and readability of the typed documents. A faded American ribbon might result in ghostly impressions, while a European ribbon, carefully crafted, could produce crisp, enduring text for decades.
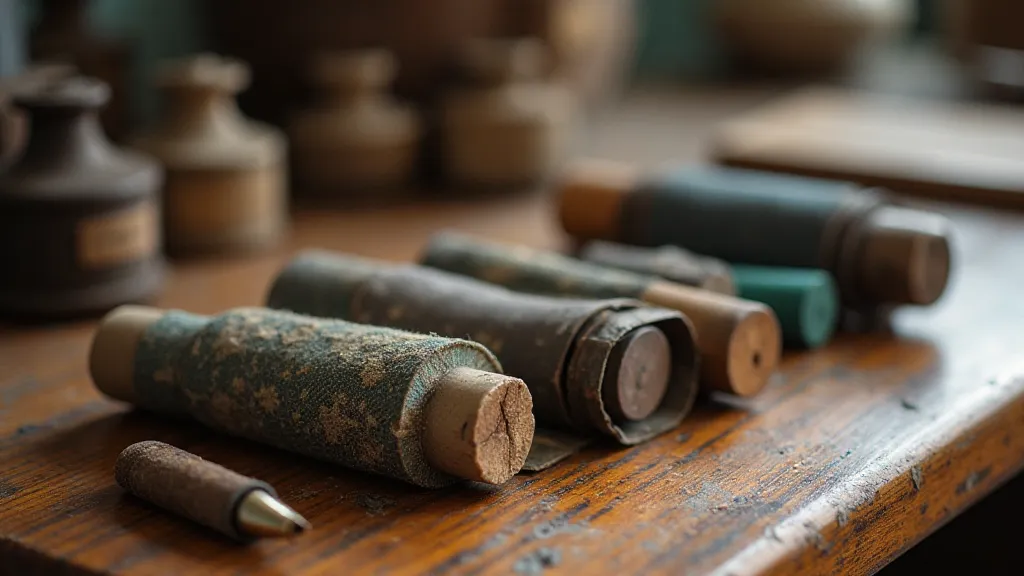
The Rise of Synthetic Fibers and Regional Specialization
The advent of nylon and other synthetic fibers in the mid-20th century dramatically altered the landscape of typewriter ribbon production. Nylon offered significantly improved durability and elasticity, leading to longer ribbon life and more consistent performance. However, the transition wasn’t uniform across the globe. American manufacturers rapidly adopted nylon, streamlining their production lines and focusing on volume. In contrast, some European workshops, fiercely protective of their traditional methods, continued to produce high-quality silk and satin ribbons, catering to a niche market of discerning typists and collectors.
Regional specialization became increasingly apparent. Germany, for example, emerged as a significant exporter of premium typewriter ribbons, particularly those intended for high-end machines like the Olympia and Imperial typewriters. These ribbons were renowned for their deep black ink, often formulated using complex mixtures of dyes and pigments. The precise formulation of these inks was a closely guarded secret, passed down through generations of ribbon artisans. France, similarly, maintained a reputation for producing ribbons with a distinctive, almost velvety texture. The subtle variations in fabric weave and ink formulation contributed to the unique character of each regional product.
I recall visiting an antique shop in Berlin several years ago, where I discovered a box of vintage Olympia typewriter ribbons. The deep black ink, the luxurious feel of the fabric – it was immediately clear that these were not your average ribbons. The shop owner, a wizened gentleman with a passion for all things mechanical, explained that these ribbons were manufactured in a small workshop near Stuttgart, using techniques that had remained virtually unchanged for over seventy years. It was a powerful reminder of the human element in industrial production, a connection to the past that transcended mere functionality.
Decoding the Marks: A Cartographer’s Guide
Identifying the origin of a typewriter ribbon can be a challenging but rewarding endeavor. The most reliable clues often lie in the manufacturer’s markings, which can vary significantly depending on the region and era of production. Early American ribbons often bear simple, stamped markings like "Smith Corona" or "Underwood." European ribbons, particularly those from Germany, frequently display more elaborate markings, including the manufacturer’s name, the ribbon type (e.g., "Satin," "Nylon"), and sometimes even the year of production.
Color variations are another crucial indicator. While black was the most common color, variations in shade and tone can reveal valuable information about the ink formulation and the manufacturing process. For instance, ribbons from the 1920s and 1930s often exhibit a slightly reddish or purplish hue, due to the use of aniline dyes. Later ribbons, produced after the introduction of synthetic dyes, tend to be a more neutral black.
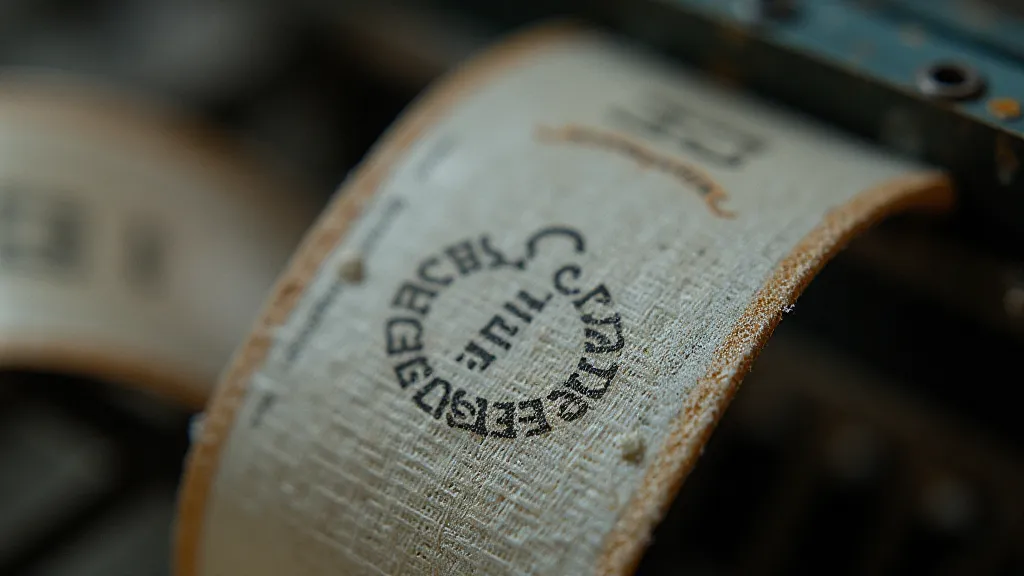
The fabric itself offers clues as well. Early silk ribbons are noticeably thinner and more delicate than later nylon ribbons. European ribbons often feel softer and more luxurious than their American counterparts. Even the way a ribbon curls or unravels can provide insights into its construction and the quality of the materials used.
The Collector’s Perspective and Preservation
For collectors of antique typewriters and typewriter paraphernalia, ribbons represent a crucial element of the historical record. A ribbon is more than just a consumable; it's a tangible link to the past, a silent witness to the words that shaped our world. Preserving these fragile artifacts requires careful handling and storage. Ribbons should be stored in a cool, dry environment, away from direct sunlight and extreme temperatures. They should be handled with clean hands to avoid transferring oils and contaminants.
The appreciation for regional variations in typewriter ribbon production is growing. Collectors actively seek out ribbons from specific manufacturers or regions, recognizing the unique historical and cultural significance they represent. The stories these ribbons tell – the echoes of workshops and families, the legacy of skilled artisans – enrich our understanding of a bygone era. Identifying those markers is not merely a technical exercise; it's an act of historical preservation, a cartographic endeavor that illuminates the landscape of industrial craftsmanship.
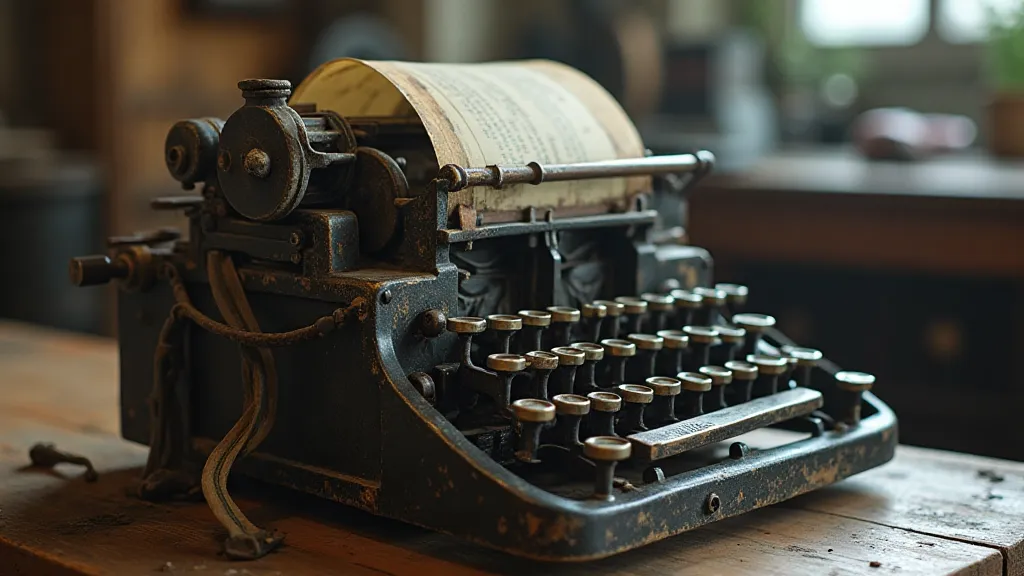
The next time you examine an antique typewriter ribbon, take a moment to appreciate the journey it has taken, the hands that crafted it, and the stories it holds. It is a small piece of history, a cartographer’s mark on the map of our past.